Custom Metal Fabrication: Tailoring Solutions for Unique Product Needs
In the ever-evolving landscape of industrial manufacturing, custom metal fabrication emerges as a pivotal process, offering tailored solutions that address the unique specifications of professional industrial buyers. This process is integral to product development, enabling the creation of metal components that are precisely engineered to fit seamlessly into larger machinery and production lines. By leveraging advanced techniques and cutting-edge technology, custom metal fabrication not only facilitates the creation of intricate designs but also ensures that these components are both functional and aesthetically pleasing. The bespoke nature of custom metal fabrication allows manufacturers to adapt swiftly to changing market demands, enhancing the quality and performance of the final product.
Custom metal fabrication involves a series of meticulously planned steps, starting with the design and engineering phase. Here, skilled engineers work closely with clients to understand their specific requirements, translating these needs into detailed blueprints and plans. The use of state-of-the-art software and tools enables precise calculations and simulations, ensuring that the final product will perform optimally under real-world conditions. Once the design is finalized, the fabrication process begins, utilizing advanced machinery to cut, bend, and assemble the metal components with unparalleled precision. This level of customization is particularly beneficial for industrial buyers who require components that are not only durable but also capable of withstanding the rigors of demanding industrial environments.
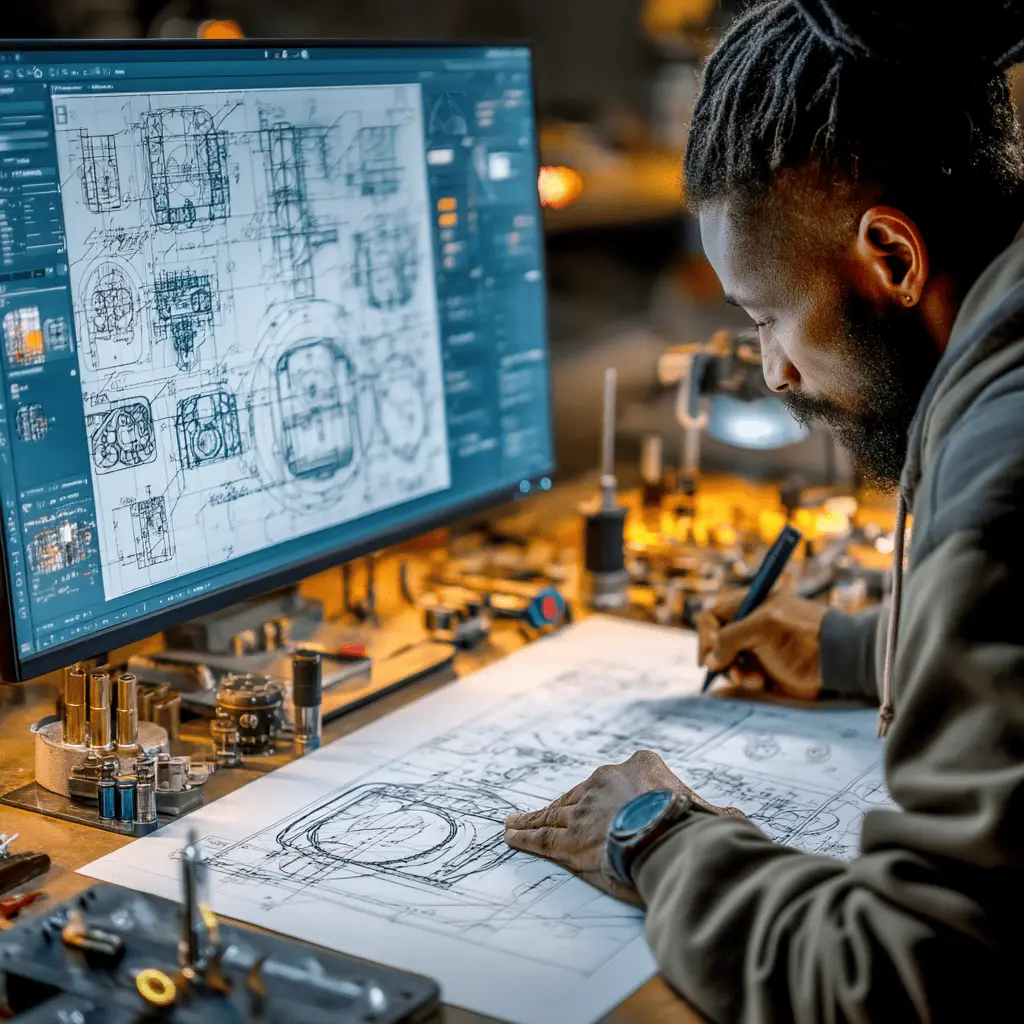
Sheet Metal Stamping: Precision and Efficiency in Component Creation
Sheet metal stamping is a cornerstone technique in the fabrication of complex metal components, renowned for its precision and efficiency. This process involves the use of high-pressure dies and presses to shape sheet metal into the desired form, making it an ideal solution for producing large volumes of identical parts. The consistency and reliability achieved through sheet metal stamping are unmatched, providing industrial buyers with durable and cost-effective solutions for their machinery and production lines. The ability to produce intricate designs with minimal material waste further underscores the value of this technique in modern product development.
One of the primary advantages of sheet metal stamping is its ability to produce components with high precision and repeatability. This is achieved through the use of advanced stamping presses, which apply consistent pressure to form the metal into the desired shape. The process begins with the creation of a die, a specialized tool that defines the shape and features of the final component. Once the die is created, it is mounted onto the stamping press, where sheets of metal are fed through and shaped with precision. This method is particularly advantageous for high-volume production, as it allows for the rapid creation of large quantities of identical parts, ensuring consistency and quality across the board.
Metal Forming Services: Shaping the Future of Product Development
Metal forming services encompass a wide range of techniques used to shape metal into specific forms and structures, playing a crucial role in the development of products that require complex geometries and high strength-to-weight ratios. These services are integral to industries that demand innovation and precision, allowing for the creation of components that meet rigorous industry standards. By employing methods such as bending, rolling, and drawing, metal forming enables manufacturers to develop products that push the boundaries of design and functionality. Industrial buyers benefit from the versatility and precision offered by metal forming services, which are essential in an ever-evolving market where adaptability is key to success.
The process of metal forming begins with the selection of the appropriate technique based on the desired shape and properties of the final component. Bending involves the deformation of metal along a straight axis, allowing for the creation of angular shapes and structures. Rolling, on the other hand, involves passing the metal through a series of rollers to achieve a specific thickness or curvature. Drawing is a technique used to stretch the metal into a desired shape, often used in the creation of complex, hollow components. Each of these techniques offers unique advantages, and the choice of method is determined by the specific requirements of the project.
Metal Stamping Process: From Concept to Finished Product
The metal stamping process is a comprehensive journey that transforms raw materials into finished products, encompassing several stages from conceptualization to production. This process begins with the design phase, where engineers and designers collaborate to create detailed plans for each component. The use of advanced software and simulations allows for the optimization of the design, ensuring that the final product will meet all specifications and requirements. Once the design is finalized, the process moves to the production stage, where advanced machinery and skilled technicians work together to stamp, shape, and assemble the parts.
Quality control measures are implemented throughout the metal stamping process to ensure that each piece meets the highest standards of precision and durability. This meticulous approach guarantees that the final product not only fulfills the intended purpose but also exceeds the expectations of industrial buyers. The ability to produce components with high precision and consistency is critical in industries where reliability and performance are paramount. The metal stamping process is a testament to the power of modern manufacturing techniques, enabling the creation of complex and innovative products that drive industrial progress.
Stamped Metal Parts: Building Blocks of Modern Machinery
Stamped metal parts are essential components of modern machinery, providing the structural integrity and functionality needed for efficient operation. These parts are created through the metal stamping process, which allows for the production of complex shapes and designs with high precision. Industrial buyers rely on stamped metal parts for their durability, consistency, and cost-effectiveness, making them a preferred choice for various applications in manufacturing and production lines. The ability to produce large quantities of identical parts ensures that machinery operates smoothly and reliably, minimizing downtime and maximizing productivity.
The versatility of stamped metal parts is one of their greatest strengths, as they can be used in a wide range of applications across different industries. From automotive components to electronic enclosures, stamped metal parts are integral to the functionality of countless products. The precision and consistency achieved through the metal stamping process ensure that each part performs as expected, providing the reliability and durability that industrial buyers demand. This makes stamped metal parts an indispensable component in the manufacturing process, driving efficiency and innovation in modern machinery.
Product Development Techniques: Innovating Through Metal Stamping
Product development techniques in the realm of metal stamping are continually evolving, driven by advancements in technology and materials. These techniques focus on optimizing the design and manufacturing processes to create products that are both innovative and practical. By integrating cutting-edge software and machinery, manufacturers can streamline production, reduce costs, and improve the quality of stamped metal parts. Industrial buyers benefit from these innovations, gaining access to products that offer superior performance and reliability. The ongoing development of new techniques ensures that the metal stamping industry remains at the forefront of product innovation, catering to the diverse needs of the market.
One of the key trends in product development is the increasing use of digital tools and simulations to enhance the design process. These tools allow engineers to visualize and test their designs in a virtual environment, identifying potential issues and making necessary adjustments before production begins. This not only reduces the risk of errors but also speeds up the development process, allowing manufacturers to bring new products to market more quickly. Additionally, advancements in materials science have led to the development of new alloys and composites that offer improved performance and durability, further expanding the possibilities for innovation in metal stamping.
High-Volume Stamping: Meeting the Demands of Large-Scale Production
High-volume stamping is a key aspect of metal stamping services, addressing the needs of industrial buyers who require large quantities of components for their machinery and production lines. This process involves the use of advanced presses and dies to produce thousands of identical parts with precision and efficiency. The ability to scale production to meet high demand is crucial for manufacturers looking to maintain a competitive edge in the market. High-volume stamping not only ensures consistency and reliability but also reduces production costs, making it an attractive option for industrial buyers seeking cost-effective solutions without compromising on quality.
The high-volume stamping process is characterized by its ability to produce large quantities of parts in a relatively short amount of time. This is achieved through the use of automated stamping presses, which can operate continuously to produce thousands of identical components. The use of automation not only increases efficiency but also ensures that each part is produced to the same high standard, providing the consistency that industrial buyers demand. This makes high-volume stamping an ideal solution for industries that require large-scale production, such as automotive manufacturing and consumer electronics.
Prototype to Product: Transforming Ideas into Tangible Solutions
The journey from prototype to product is a transformative process that turns innovative ideas into tangible solutions. In the context of metal stamping services, this journey involves several stages, from initial design and prototyping to final production and quality assurance. Prototyping allows manufacturers to test and refine their designs, ensuring that the final product meets all specifications and requirements. Once the prototype is perfected, the transition to full-scale production begins, leveraging the capabilities of metal stamping to create high-quality components efficiently. This seamless progression from concept to reality is vital for industrial buyers seeking reliable and effective solutions for their machinery and production lines.
The prototyping phase is a critical step in the product development process, allowing manufacturers to test and validate their designs before committing to full-scale production. This involves creating a small-scale version of the product, which can be used to assess its performance and identify any potential issues. By making adjustments during the prototyping phase, manufacturers can ensure that the final product will meet all specifications and requirements. Once the prototype is finalized, the transition to full-scale production begins, utilizing the capabilities of metal stamping to produce high-quality components efficiently and cost-effectively. This seamless progression from prototype to product is essential for industrial buyers seeking reliable and effective solutions for their machinery and production lines.