ABS Plastic Material: Understanding Its Role in Modern Manufacturing
ABS plastic, or Acrylonitrile Butadiene Styrene, is a widely used engineering thermoplastic known for its versatility and cost-effectiveness. It is a popular choice in a variety of industries due to its excellent balance of properties, including impact resistance, toughness, and ease of processing. As a professional in the industrial sector, understanding the applications and benefits of ABS plastic can significantly enhance your material selection process.
ABS is commonly used in automotive parts, consumer electronics, and even in the construction industry. Its ability to withstand physical impacts makes it ideal for products that require durability. Furthermore, ABS plastic can be easily machined and molded, offering flexibility in design and manufacturing processes. As you navigate the landscape of plastic materials, recognizing the strengths of ABS can inform your decisions and optimize your production line.
The adaptability of ABS plastic extends beyond its mechanical properties. Its aesthetic qualities, such as its capacity to achieve a smooth and glossy finish, make it suitable for consumer-facing products where visual appeal is crucial. The ease of coloring and surface treatment further enhances its desirability in industries where branding and product differentiation are important.
In addition to its practical applications, ABS plastic is also a subject of ongoing research and development. Innovations in ABS formulations are continually improving its performance characteristics, such as heat resistance and environmental sustainability. Professionals who keep abreast of these developments can leverage new ABS variants to meet evolving industry standards and consumer expectations.
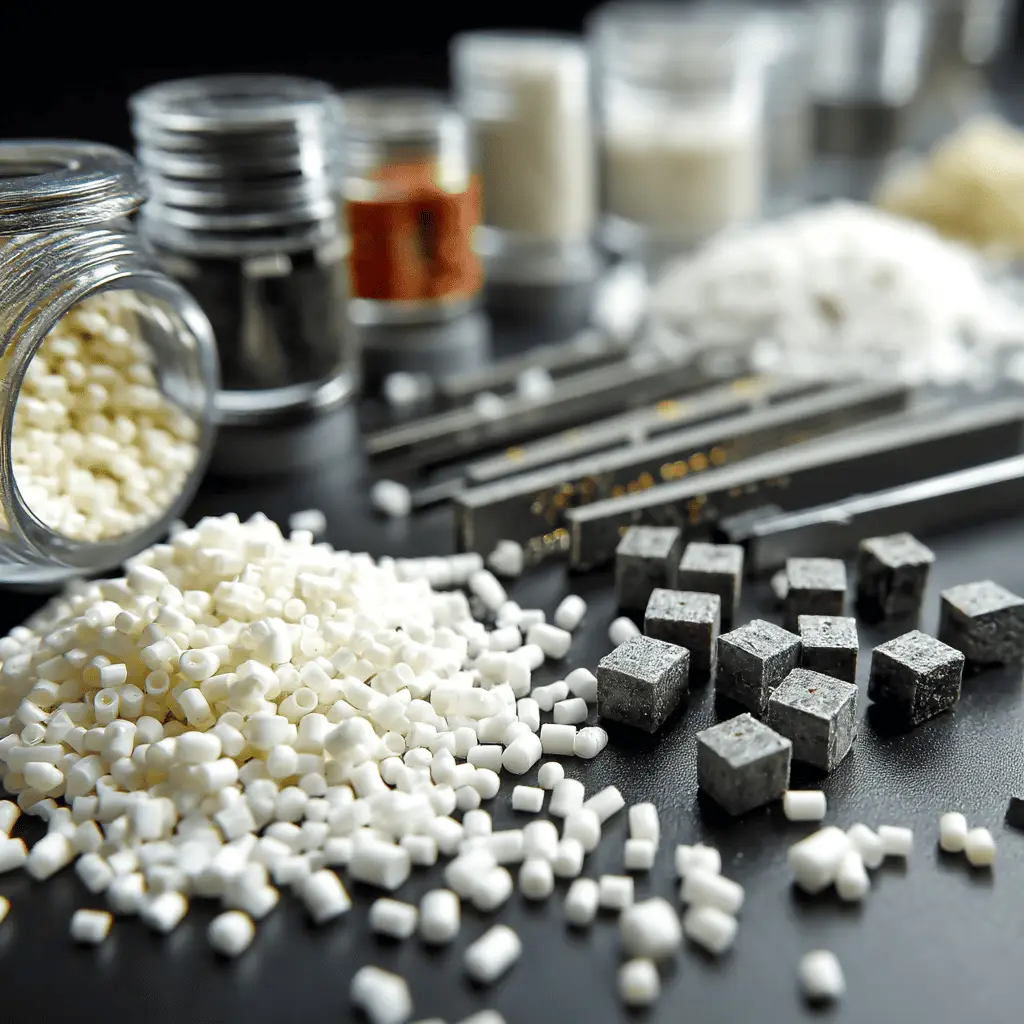
ABS Material Properties: Key Characteristics for Industrial Applications
The properties of ABS plastic make it a favored choice among professionals seeking reliable materials for their projects. Its high impact strength ensures that products can endure rough handling and resist breakage, which is crucial in sectors like automotive and electronics. Additionally, ABS exhibits good dimensional stability, meaning it maintains its shape and size under various conditions, providing consistency in product quality.
ABS plastic also offers excellent surface finish capabilities, allowing for aesthetically pleasing products with minimal post-processing. Its chemical resistance to acids and alkalis further extends its applicability in harsh environments. Understanding these properties enables professionals to effectively leverage ABS plastic in applications where durability and appearance are paramount.
Another significant property of ABS is its thermal stability. While not as heat-resistant as some high-performance polymers, ABS can withstand moderate temperatures, making it suitable for applications that experience occasional heat exposure. This property is particularly beneficial in the automotive industry, where components may be exposed to varying temperatures.
Moreover, the electrical insulation properties of ABS plastic make it an excellent choice for electronic housings and components. Its ability to insulate against electrical currents ensures the safety and reliability of electronic devices, further broadening its utility across different sectors. By understanding the multifaceted properties of ABS, professionals can make informed decisions that enhance the quality and performance of their products.
Advanced Plastic Materials: Exploring Innovations in Polymer Technology
In the realm of plastics, advancements in material science have led to the development of high-performance polymers that cater to specialized needs. These advanced plastic materials surpass traditional options in terms of strength, heat resistance, and chemical stability. For professionals navigating the complex landscape of plastic materials, staying informed about these innovations is essential.
Materials such as polyether ether ketone (PEEK) and polyphenylene sulfide (PPS) offer remarkable properties that make them suitable for demanding applications, including aerospace, medical devices, and industrial machinery. These advanced plastics provide solutions where conventional materials fall short, allowing for the creation of products that can withstand extreme conditions and perform reliably over time.
The development of advanced plastics is driven by the need for materials that can meet stringent performance criteria while also addressing environmental concerns. Biodegradable and recyclable polymers are emerging as viable alternatives to traditional plastics, offering sustainability without compromising on quality. Professionals who integrate these materials into their production processes can align with global sustainability goals and enhance their brand reputation.
Furthermore, advancements in polymer technology are opening new avenues for customization and specialization. Tailor-made polymers that address specific industry challenges, such as high-temperature resistance or enhanced flexibility, are becoming more accessible. By adopting these innovations, professionals can create products that not only meet but exceed market expectations, ensuring a competitive edge in their respective fields.
Polymers in Engineering: The Backbone of Modern Manufacturing
Polymers play a pivotal role in engineering, serving as the backbone of modern manufacturing processes. Their versatility and adaptability make them indispensable in the creation of components across various industries. As a professional industrial buyer, understanding the significance of polymers in engineering can guide material selection and enhance your production line efficiency.
Engineering polymers like nylon, polycarbonate, and polyethylene are known for their mechanical strength and thermal stability. These materials are employed in applications ranging from automotive parts to electrical components, offering solutions that meet specific performance criteria. By leveraging the diverse capabilities of polymers, professionals can design and manufacture products that cater to the evolving demands of the market.
The integration of polymers into engineering practices is not limited to their mechanical properties. Their chemical resistance and lightweight nature make them ideal for applications where weight reduction and corrosion resistance are priorities. This is particularly evident in the aerospace and automotive industries, where reducing weight without compromising strength is a constant challenge.
Moreover, the ability to modify and enhance polymer properties through additives and composites further expands their application potential. By combining polymers with other materials, engineers can create hybrid solutions that offer improved performance and durability. This flexibility in material design allows for innovation and optimization in manufacturing processes, ultimately leading to more efficient and cost-effective production lines.
PEEK Plastic Introduction: Unveiling Its High-Performance Features
Polyether ether ketone (PEEK) is a high-performance polymer renowned for its exceptional properties. It is often chosen for applications that require superior strength, heat resistance, and chemical inertness. As professionals seek materials that can withstand rigorous conditions, PEEK stands out as a premium choice.
PEEK plastic is used in industries such as aerospace, automotive, and medical devices, where reliability and durability are non-negotiable. Its ability to maintain mechanical properties at high temperatures makes it ideal for components that experience thermal stress. Additionally, PEEK’s resistance to chemicals and radiation further broadens its applicability, offering solutions for challenging environments.
The high-performance attributes of PEEK are complemented by its machinability and versatility in processing. It can be easily fabricated into complex shapes and structures, making it suitable for intricate components that require precision. This characteristic is particularly valued in the medical field, where PEEK is used to produce implants and surgical instruments that demand exacting standards.
Furthermore, PEEK’s biocompatibility makes it a preferred choice for medical applications, as it does not elicit adverse reactions when in contact with human tissue. This property, combined with its mechanical and thermal stability, positions PEEK as an indispensable material in the development of advanced medical devices and implants. Professionals who utilize PEEK in their projects can deliver products that meet the highest standards of safety and performance.
PEEK vs ABS Plastics: Comparing Performance and Applications
When choosing between PEEK and ABS plastics, professionals must consider the specific requirements of their projects. While both materials offer unique advantages, their properties and applications differ significantly. ABS plastic is favored for its cost-effectiveness and ease of processing, making it suitable for consumer products and automotive components where impact resistance is crucial.
On the other hand, PEEK plastic is selected for high-performance applications that demand superior mechanical and thermal properties. Its ability to operate at elevated temperatures and resist chemical exposure makes it ideal for aerospace and medical applications. By understanding the strengths and limitations of both materials, professionals can make informed decisions that align with their project goals.
The decision between PEEK and ABS often comes down to a balance of performance and cost. While PEEK offers unparalleled performance in demanding environments, it is also more expensive than ABS. Therefore, professionals must weigh the benefits of PEEK’s enhanced properties against the budgetary constraints of their projects. In applications where the highest levels of performance are not necessary, ABS provides a cost-effective alternative that still meets essential criteria.
Moreover, the choice between PEEK and ABS can also be influenced by environmental considerations. The production processes and recyclability of each material differ, and professionals must consider the environmental impact of their material choices. By evaluating the lifecycle and sustainability of PEEK and ABS, professionals can make decisions that support both their project objectives and environmental responsibilities.
Overview of Plastic Materials: Navigating the Vast Landscape
The world of plastic materials is vast and diverse, offering solutions for a multitude of applications. From everyday consumer products to specialized industrial components, plastics play a critical role in modern manufacturing. For professionals navigating this landscape, understanding the various types of plastics and their properties is essential for successful material selection.
Thermoplastics, thermosets, and elastomers each offer distinct characteristics that cater to different needs. Thermoplastics like ABS and polycarbonate are known for their recyclability and ease of processing, while thermosets such as epoxy provide excellent chemical resistance and structural integrity. Elastomers like silicone offer flexibility and resilience, making them suitable for applications requiring elasticity.
As professionals explore the landscape of plastic materials, it is important to consider the evolving trends and innovations that shape the industry. The demand for sustainable and environmentally friendly plastics is driving research into biodegradable polymers and recycling technologies. By staying informed about these developments, professionals can make material choices that align with industry trends and consumer expectations.
Additionally, the integration of digital technologies in material selection processes is transforming how professionals navigate the plastic materials landscape. Tools such as material databases and simulation software enable more precise and efficient decision-making, allowing professionals to evaluate materials based on specific performance criteria and project requirements. By leveraging these technologies, professionals can streamline their material selection processes and enhance the overall efficiency of their production lines.
Plastic Materials Navigation: A Professional’s Guide to Material Selection
For industrial buyers and professionals in the manufacturing sector, navigating the complex world of plastic materials requires a strategic approach. The selection of the right material can significantly impact the performance, cost, and sustainability of a product. By understanding the properties of various plastics and their applications, professionals can optimize their material choices and enhance their production processes.
Factors such as mechanical strength, thermal stability, chemical resistance, and cost-effectiveness must be considered when selecting plastic materials. Additionally, advancements in polymer technology continue to introduce new materials with enhanced capabilities, providing professionals with a broader range of options. By staying informed and leveraging the strengths of different plastics, professionals can successfully navigate the landscape and achieve their project objectives.
Effective material selection also involves considering the long-term implications of material choices. Professionals must evaluate not only the immediate performance and cost benefits but also the lifecycle and sustainability of the materials they choose. By adopting a holistic approach to material selection, professionals can ensure that their products meet current standards while also preparing for future challenges and opportunities.
Ultimately, the ability to navigate the plastic materials landscape effectively can provide professionals with a competitive advantage in the marketplace. By making informed and strategic material choices, professionals can deliver products that meet the highest standards of quality and performance, ensuring success in their respective industries.